Product overview
MIR-71000 Mirror Silver is a mirror ink for screen printing with excellent printability on polycarbonate and treated PET materials. It offers environmental and cost advantages as an alternative to plating, and can be applied to home appliances, mobile phones, and other products.
- Functional ink
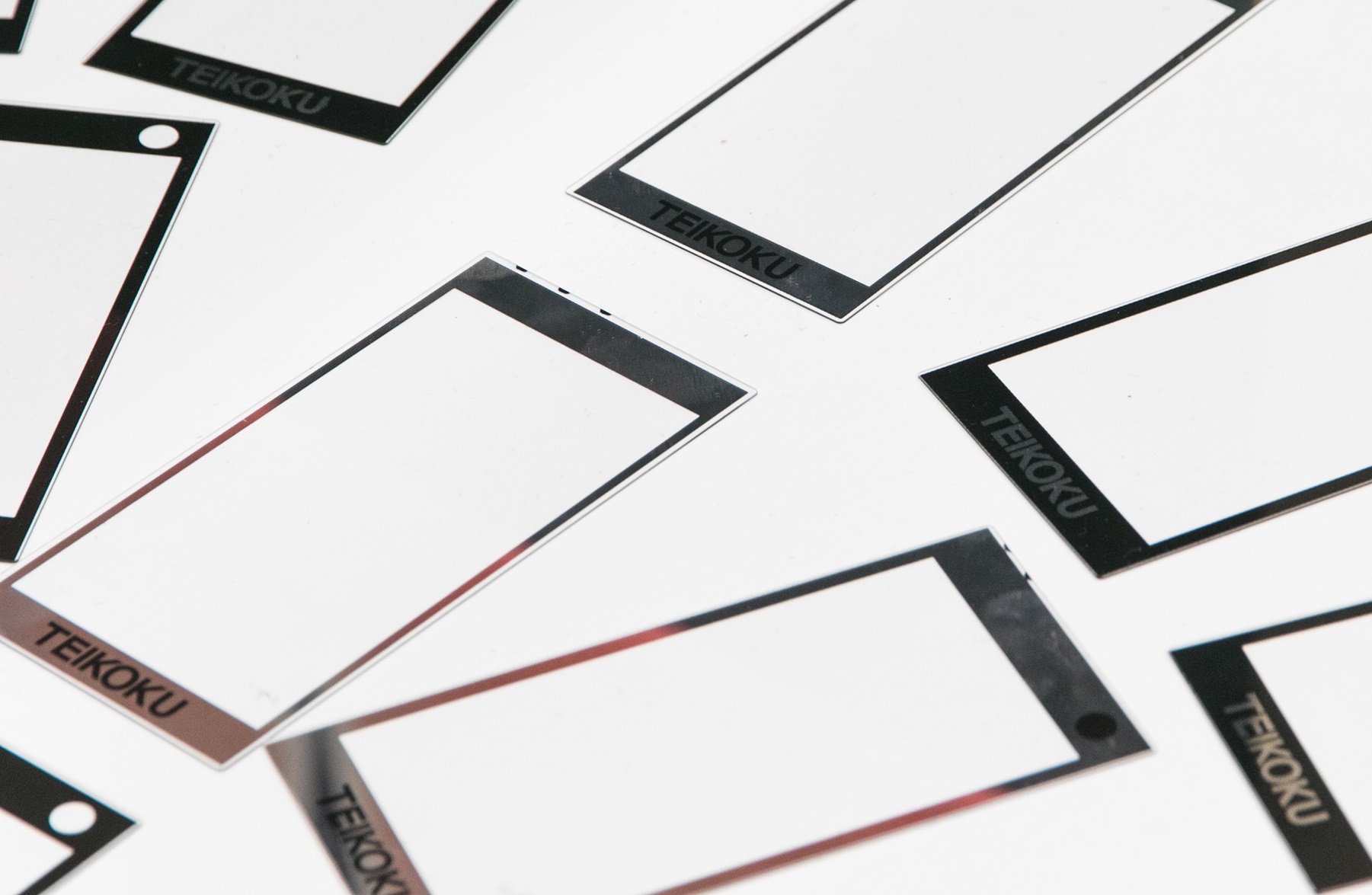
Application
- Display panels for home appliances, membrane switches
-
Automobile, Motorcycle
-
Home Appliance (IoT)
-
Smartphone, Tablet, Smart watch
-
Sensor
-
Game
-
Others
Features, Function
- No intentional use of Halogen (Chlorine Cl, Bromine Br) compounds in raw materials.
- High thixotropy, suitable viscosity for printing, and excellent printability.
- Mirror
Substrate
- PC and Treated PET film
- PC
- Easy adhesion treated PET
Dilution
- C-002 SOLVENT
- Dilution: 0 to 10%
- *Basically, no dilution is needed. Do not use other solvents as they may adversely affect mirror surface, adhesion, stencil stability, and other properties.
Catalyst, Promoter mixing
- 106 CATALYST 1% (to improve adhesion) Pot life: 4 hrs.
- 200 CATALYST 3% (for insert molding) Pot life: 4 hrs.
- *Use catalyst to improve adhesion to hard-to-bond substrates (hard coat substrates, etc.) and for insert molding applications. Please mix only the amount to be used.
Recommended cleaner
- Screen Cleaner L2
Mesh
- T 300 mesh (Coverage is about 40-50m2/kg)
Drying
- 80°C 30 min
- Over print
MIR 80°C 30 min
Back print 80℃ 30 min
Caution
- Although Mirror Ink itself adheres to the substrate, be sure to overprint to prevent scratch and to improve gloss and resistance.
- Use “MIX-HF or MIB Ink series” for back print. For recommended printing conditions, please refer to the respective ink catalog.
- If the ink layer thickness is 3μm or more, delamination may occur between mirror ink and back print ink.
- Heated drying is strongly recommended. More than 30 min at 80°C is necessary. Delamination may occur if MIX-HF or MIB ink is back-printed and dried without the mirror ink having dried.
- Be sure to conduct preliminary tests to check the mirror surface and adhesion before carrying out mass production tests.
- Ink viscosity increases after printing. Do not add used recovered ink to unused ink, transfer it to another container, add C-002 solvent to dilute the ink up to the viscosity of unused ink before use. However, when using recovered inks,please check the print finish, etc. in advance.
- Ink shelf life: 6 months from production date, unopened.
Safety
- UN No.: Not classified in the definition
- UN Classification: Not classified in the definition
Handling
- Use safety gloves and eyeglasses to protect skin and eyes. If the ink comes in contact with skin, wash with soap and plenty of water (or lukewarm water) and consult with a doctor.
- Containers should be closed tightly after use and stored in a cool and dark place.
- SDS is available upon request. Please request a copy and read it carefully before handling the products.
- *Information contained in this catalog may change without prior notice.
FAQ
-
Is it possible to add color to mirror ink?
-
Mirror inks are available in a variety of colors. Vivid colors and high mirror effect can be achieved by combining with transparent ink. Please refer to the following to select the ink that best suits your application.
Related link
Introduction of MIX-HF (1)
Introduction of TOC-HF transmittance ink (2) -
When drying the print in a line oven it sometimes appears hazy. Why does this occur?
-
Upon further investigation with the customer, the printing conditions that caused this hazy appearance were discovered to be as follows. Mirror Ink was printed with a cylinder press and dried in a line dryer at a high temperature, thus the resultant hazy effect. The reason being: the initial drying at a high temperature. The recommended drying condition is 30 minutes at 80°C, but in this case the line dryer was used for 2 minutes at 100°C. When the substrate was dried at this high temperature with a great deal of solvent on it, the substrate was affected adversely and turned white.
- Related technical information